

APPROPRIATE TECHNOLOGY FOR THE WORLD'S PEOPLE, DESIGN
Immersion
Heater

Problem
The people of Uganda (and other nations, coming to a total of 3 billion people worldwide) currently cook most of their food over a wood/biomass fire inside of their home. The smoke emissions from this fire causes about 4 million deaths per year. The emissions are also harmful to the environment, speeding up global warming by emitting carbon dioxide and soot.
​
We need to create a healthier, cleaner way for the people of Uganda, and other developing nations, to cook their food.



Background
Affordable and effective immersion heaters exist already, but we cannot buy them because they must have the perfect resistance to maximize the power output from the solar panel. The voltage and current that the solar panel operates directly dictates the power it provides. The resistance of the heating element will dictate the operating voltage. Therefore, the heating element can limit the power that the solar panel can provide. Also, most manufacturers currently use very advanced machinery that the people of Uganda will not have access to. Therefor we would also like to create a simple, step by step manufacturing process. In addition, adding phone charging capabilities will increase the demand for and use of these heaters.
If people can create these in their local villages without machinery and industry, we can create local economies and spark innovation.

Solution
To do this, we are making a heating element. Specifically, we are making a food grade immersion heater to be powered by a 100 Watt solar panel and immersed in an insulated pot, allowing people to use solar energy to slow cook various foods and boil water. This aligns with their current method of cooking, which is boil and simmer.

Our Team
Matthew Walker
Amanda Stahler
Micaela Board
BACKGROUND
2015: Founded Shady Tree Shades - a small business selling eco-friendly apparel. 2016: Designed & Manufactured a Tensile Strength Tester for QL+ Club. Summer 2017: Worked for Tesla Energy selling home solar systems. Fall 2017 – present: Leading a team of researchers on Immersion Heater R&D + Manufacturing under advisor Dr. Peter Schwartz.
EXPERTISE
+ 3D Modeling (Solidworks)
+ Basic Manufacturing/Electrical/
Materials Engineering
+ Sales
+ Marketing (online especially)
BACKGROUND
Graduating this June with a Bachelors of Architecture and a minor in Italian Studies and Sustainable Environments. Spent the last year studying architecture abroad in Florence, Italy and will be working for an architecture firm in the Bay Area after graduation. Currently designing a Women’s Opportunity Center in Rwanda for senior thesis through the humanitarian organization Journeyman International.
EXPERTISE
+ Architectural and
sustainable design
+ Graphics
+ Digital modeling
+ Welding
+ Knowledge on culture and
infrastructure in Rwanda
BACKGROUND
Graduating Fall 2018 with Bachelors in Communication Studies. Associates Degree in Speech Communications. Working with a hospitality business to improve guest communications. Create marketing plans for local musicians and artists.
EXPERTISE
+ Intercultural Communications
+ Marketing Strategies
3RD YEAR:
SUSTAINABLE ENERGY ENGINEERING
5TH YEAR:
ARCHITECTURE
5TH YEAR:
COMMUNICATION STUDIES
Jessica Wei
BACKGROUND
Concentrating in Web & Digital Media but hoping to switch over to Design Reproduction Technology. Goal is to go into product design or the advertisement industry. Currently developing a passion project called Vistal, a magazine featuring music and art.
EXPERTISE
+ Layout Design
+ Image Retouching
+ Branding
+ UX / UI
+ Advertising Design
+ CSS / HTML
2ND YEAR:
GRAPHIC COMMUNICATION
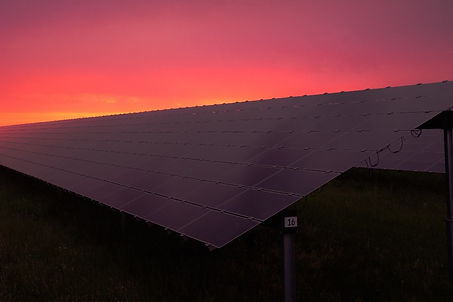
Progress
​
Week 4
Week 5
Week 1
Week 2
Week 3
Week 6
Week 8
Week 7
Week 9
Week 10
Next Steps
Introduction to Class
Appropriate Technology for the World's People: Design
Group Formed
Matt, Amanda, Micaela, Jessica
Composite Samples


Finding the best ratio for Magnesium Oxide to Cement/Gypsum to Water in order to maximize electrical resistivity and thermal conductivity. 2 groups of 3 different ratios. Group 1= Cement, Group 2= Gypsum. Total of 6 different samples. Tested at a later date, we found the 10:1 MgO:Cement to be the most thermally conductive.
Soldering Diodes



Testing the voltage between each diode to ensure that the electrical connection is intact. Lead-Tin solder (350 F or higher melting point) is used to solder diodes in series.
Manufacturing Progress
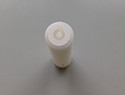

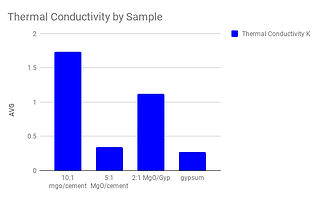
3D Modeled and printed molds to create life-saver candy shaped disks of composite that will allow for easier manufacturing. This failed because gypsum expanded inside the molds, so we were unable to remove the gypsum from the molds without breaking it.
Thermal Conductivity Measurement
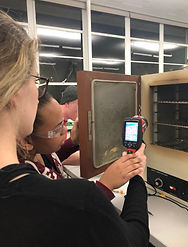

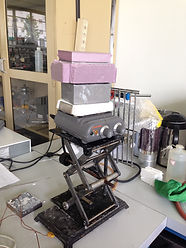
The first attempt to measure the specific heat each of the composites failed. The idea was to heat all of the composites up to the same temperature and then drop them in water to see which retained heat the longest.
In the end we used a thermal conductivity measurement device which has two insulated chambers (one of boiling water on the bottom and one with ice on the top) the composite is then placed in between the two chambers. The heat must travel from the boiling water through the composite into the ice. You measure the time it takes to melt the ice, mass of ice and water, and temperature difference between the top and bottom of the composite which is plugged into a computer calculator to find the k value (thermal conductivity constant) of that specific composite.
Composite Ratio Charts
Begin Prototyping

Used the drill press in Bonderson for the 1/2" through hole to fit the 3/8" copper tubing.
​
Results from composites created previously.
10:1 MgO:Cement is has the highest thermal conductivity. of ~2W/m*K
Variation of Immersion Heater
We used nichrome wire and pure gypsum insulation in a 3 foot long thick walled steel tube.
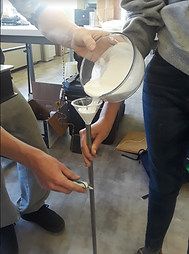
Gypsum insulation pouring


Bending the 3 foot steel tube
Finish Prototyping + Process Improvements



MANUFACTURING PROCESS
​
Materials:
1. 1N5408 Diodes (~21 for 18 volts)
2. Soldering Kit (soldering iron + solder)
3. Insulated copper wire (~3ft)
4. Wire stripper or cutter
5. Thin walled copper tubing (~3/8" OD, 1/4" or larger ID)
6. Hand held tubing bender (optional)
7. Magnesium Oxide powder (50-100g)
8. Cement powder (portland, 5-10g)
9. Water (100-200g)
10. Mixing container
11. Funnel
12. Vibrating toothbrush (optional)
13. JB weld or any food-safe epoxy (melting temperature over 300C)
14. Voltmeter (optional - for testing 5 volt node)
​
Instructions:
1. Solder a string of diodes closely in series (1/2" of spacing between or less) as shown in "Solution" figure above. At the 5 volt node, solder a copper wire long enough to reach the end of the tube. This node can be found using a voltmeter, or you can estimate it to be 6 diodes away from ground. This wire will be used to charge a phone. At each end of the diode chain, solder copper wires to serve as leads to the power source. All copper wiring should be insulated anywhere they are not electrically connected in order to prevent shorting.
​
2. Place the diode string inside the copper tubing such that there is the same length of copper lead inside of each end of the tube as shown in "Solution" figure above.
​
3. Bend to fit into a Hydroflask (opening = 2.1" diameter) using a hand held tubing bender, or by hand. Try not to make any kinks in the tube as this could cause shorting.
​
4. Create composite by adding 10 grams of MgO to every 1 gram of cement, and mixing dry. Next, add water little by little and mix as you go until your composite is the consistency of whole milk.
​
4. Fill the tubing with composite. A funnel can aid pouring and touching the tube with a vibrating toothbrush helps air bubbles escape.
5. After 4 days, seal the ends of the tube with JBquick or any food safe epoxy. You are ready to cook with solar!
Testing

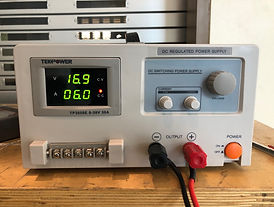
Testing the heater using a vacuum insulated bottle and 1 liter of water. Attempting to keep the power provided at a constant 100 watts from the power source, we boiled a liter of water in 50 minutes!
Testing the heater using a vacuum insulated bottle and 1 liter of water. Attempting to keep the power provided at a constant 100 watts from the power source, we boiled a liter of water in 50 minutes!
Product Developent
Next Steps Will Include:
1. Testing with a Solar Panel
2. Adding a female USB
3. Adding another wire for lighting
4. Creating an affordable insulated pot to pair with the immersion heater
5. Test Longevity
6. Add a dial to allow user to activate more diodes once they heat up and drop in voltage
User Persona


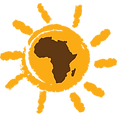
Traditional Ugandan Cuisine
STAPLE STARCH
MAIN DISHES

UGALI
-
dish made of different flours (maize, millet, cassava, or sorghum flour)
-
cooked in boiling liquid
(water or milk) -
cooked until it reaches a dough-like consistency
-
when it is cooked as porridge, it is called uji
-
usually served with salad

LUWOMBO
-
stew of either chicken, beef, mushrooms or fish
-
steamed in banana leaves
-
made for holidays or special occasions
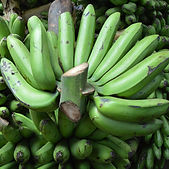
MATOOKE
-
uses green bananas (not plaintains)
-
boiled or steamed then mashed
-
cooked in/served with a peanut sauce
-
eaten with beans, fresh fish, or meat

KATOGO
-
usually made for breakfast
-
fried plantains with soup and beef, beans or offals
-
sauce is poured over and left to simmer
-
served with vegetables